The Planning Report has long covered the growth of the clean energy economy, and the developing workforce on the front lines of integrating advanced cleantech into the built environment. In Los Angeles, a portion of that workforce is led by Mike Silvey, business manager of Ironworkers Local 433. He sat down with TPR to discuss how the building and construction industries are responding and adapting to advanced technologies, as well as the role of unions in preparing the next generation of skilled workers. Kelly Candaele, a former LA Community College District trustee and respected journalist, also joins the conversation to offer his own insights gleaned from his latest documentary Heads, Hands and Hearts, which tells the stories of the construction workers building the Wilshire Grand tower in Downtown Los Angeles.
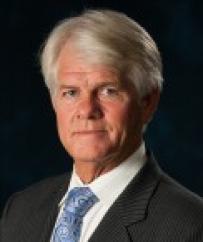
Mike Silvey
“Building technologies, welding methods, and geometry of the structures are not getting any less complex. Ironworkers have to have increasingly greater grasps of mathematics, metallurgy, the dynamics of physics, and how to work.” - Mike Silvey
How has construction work involving steel changed since you joined the Ironworkers decades ago?
Mike Silvey: The technology we use has changed. Welding methods are better, and there are better alloys. Structures also tend to be designed better.
There have been a great many improvements over time, but the single greatest one—and the one closest to home—is safety. Working at these heights is a serious hazard, and we used to lose too many ironworkers to falls. Now our guys go home safely at night to their families.
Kelly Candaele: What does the future portend for Local 433 and the construction economy? Will there be new building technologies that will dramatically change the way ironworkers do their jobs?
Mike Silvey: Not in the short term. There’s been much ado about the loss of manufacturing and the effects of NAFTA and potentially the TPP. But people that I talk to say, “We lost manufacturing? Oh, well. It’s all going to be replaced with robots anyway. And when that happens, then perhaps manufacturing will start to come back onshore, because we’ll need the software and technical skills.”
The construction economy is not going to change a great deal. Prefabrication has basically come as far as it can. That’s not even really a new technology; it depends mostly on logistics.
There may be different ways to erect structures. But it’s all going to require guys crawling around on the iron, doing the welding, and sticking the bolts in. It would take someone a lot more intelligent than I to figure out a way around that.
The ironworkers union, especially Local 433, is clearly quite proud of its apprenticeship programs that train the next generation of ironworkers. Share with us for whom and how they work.
Mike Silvey: The apprenticeship program is class time. It takes four years of classes and fieldwork—spread over eight six-month periods—for apprentices to graduate the program and become journeymen. At this time, about 750 apprentices are associated with Local 433.
Our work can be very technical. Building technologies, welding methods, and geometry of the structures are not getting any less complex. Ironworkers have to have increasingly greater grasps of mathematics, metallurgy, the dynamics of physics, and how to work each generation of new cranes and machinery. There’s a lot to know.
We watch the apprenticeship program closely, because these guys will eventually be out there on those beams, hoisting 100-ton objects over where people live. Not to be too dramatic, but our guys are responsible for their own lives and the lives of others—and they need to be able to handle it when they’re put in that position.
Community colleges and K-12s, in the past, also had a role in preparing the construction economy’s workforce. When did their participation in training decline, and the union’s grow?
Mike Silvey: That’s a tough question. We used to have a lot of collaboration. But there were funding issues, and now we have to train our own people.
We do take some applicants from the community colleges. We work with them essentially as pre-apprentices—people with potential to eventually be successful in our trade.
Kelly, you served on the board of the Los Angeles Community College District for more than 15 years. Can you speak to efforts being made to rebuild the workforce training relationship between unions and community colleges?
Kelley Candaele: If you want a template for how to restructure a program that was on the decline, look to Los Angeles Trade Technical College.
LATTC President Larry Frank—who came out of Antonio Villaraigosa’s mayorship, and before that was active with unions throughout LA—is successfully rebuilding relationships with trades in and around Los Angeles. He’s connecting the building trades up to the college, in part by inviting business managers like Mike to their classes.
Rebuilding a structure like that doesn’t happen by magic. It happens through day-to-day hard work, and getting people together to talk about how to cooperate.
Local 433 is partnering with ReNewAll to deal with the thousands of buildings in this region that need seismic retrofitting. How are you approaching this challenge?
Mike Silvey: When we start talking to building owners about retrofitting, most are somewhat resistant because of the financial implications. They’re not sure they can afford to complete a retrofit, let alone to get high enough rents out of the building after investing the money.
But the work needs to be done; it’s mandated by the city. So ironworkers are trying to make it easier for building owners to do it.
What we do with ReNewAll is find funding sources—low-interest money that can aid these building owners to help them retrofit the structures. We also offer them designs that have worked on other buildings, because it’s less expensive if they don’t have to start from zero.
In essence, we introduce them to a revenue source as well as an engineering resource, and make them a part of a community of building owners looking for common solutions.
The public may not differentiate among types of labor unions in terms of public-sector versus private-sector. But Mike, you’ve demonstrated your Local’s focus on ensuring your employers do well in a competitive economy—a somewhat different agenda than that of the public-sector unions that dominate the membership of County Federation of Labor. What leverage within the Federation do the private-sector and craft unions have to enact policies that benefit ironworkers and similar unions?
Mike Silvey: The numbers of firefighters, teachers, police officers, etc. completely overwhelm the number of people in the construction trades. While our concerns may be valid—and very important to our own membership --if the numbers are not there, then we will be overshadowed.
I don’t want to diminish the concerns of the public sector, but the fact is that we operate very differently. Our contractors, our negotiations, and our wages have to be competitive in order for our workers to get the job, make money, stay in business, and provide a middle-class Los Angeles lifestyle for their families.
We are obligated to make that happen, and there is no government funding to help us. Neither Governor Brown nor Mayor Garcetti is going to give any money to our contractors or to us. It’s all in the bid—and we must make that bid. There is no line item in the state budget to provide raises for the Ironworkers.
Kelly Candaele: Craft union members work in a competitive environment. As a result, you always have to be thinking, on one hand, about the livelihoods of your members and how to get them better wages and benefits; and on the other hand, about the health of the private companies that are putting you to work.
I was at the County Federation of Labor under Bill Robertson, when Jim Wood was the head of the CRA—when Downtown Los Angeles was being built. I don’t want to get all nostalgic and misty-eyed about this, but I think there was a better balance between public and private sector unions then. Two examples are the Machinists and the United Auto Workers who both had significant memberships here at the time.
The public sector represents their members as effectively as they can, exactly as they are supposed to. But 94 percent of the private sector is unorganized. That’s where the work and the growth need to happen if the labor movement is going to survive and have a broader economic impact.
As the national election approaches in November, there has been much commentary on the disaffection of the middle class. Mike, from your perspective at the head of a craft union, can you contextualize that discontent? What kind of policy platform would help to reengage those voters?
Mike Silvey: We’ve seen a big movement nationally called Right to Work, which labels union dues as a tax, and that propaganda has influenced many against union membership.
I would love a platform á la Upton Sinclair’s End Poverty in California movement in 1934. The way the working class is treated has declined so much over the last 40 years. People don’t realize it; it’s becoming the norm. But it doesn’t have to be this way.
Unfortunately, it seems that people won’t stand up and fight until they literally have nothing left to lose—until they realize they’re never going to make it like this. That’s when Bernie Sanders’ revolutionary talk comes in.
Mike, you grew up in Kansas, and you’ve had quite a journey to get to be the business manager of one of the largest craft unions in the country. Share your background with our readers.
Mike Silvey: I started out in the small town of Hutchinson, Kansas. I went to public school—a little high school in Nickerson, Kansas—then to Kansas State University, where I actually studied veterinary medicine for three years.
I switched to the University of Colorado to study engineering, and along the way, I joined the Ironworkers Union to make money for school. After I graduated in ’83 and worked in engineering for a little while, I found out I could make more money doing ironworking than engineering. So guess what? I was back in the field. I accepted a project in Chicago, and I never looked back.
From there, it was off to London, Paris, Munich, Africa, Hong Kong, and all across the United States and parts of Canada. I was enjoying that work, but a contingent of my brother Freemasons encouraged me to run for business manager of the union, and I decided to do it.
You see, ironworkers have a very close bond—like family, even father/son relationships. My own father is not with us anymore, but I had a great deal of respect for him. He introduced me to the trade, and since that had been good for me, I thought it was my turn to give something back.
About four years ago, I was elected to head up the Ironworkers Union here in Los Angeles and Las Vegas for the first time, and I was reelected last year. It has been quite a journey.
Kelly, you are currently working on a film that involves interviewing the craftsmen working on the Wilshire Grand high-rise. Many of the conversations you’ve recorded capture workers’ family connections, as well as relationships with their union. What have you learned about what drives skilled craftsmen, and what they value?
Kelly Candaele: I think there are a lot of misconceptions about construction workers in general, and maybe ironworkers in particular, that have been perpetuated in the media because they’re easy clichés to trade upon.
During filming, I made it a point to visit workers’ homes, because that’s where you find out about why someone would do this work—this work that sacrifices your body.
I wanted to make it clear to people that it is a tremendous sacrifice. Most of the folks working in construction aren’t going to be able to do it for 40 years. It simply doesn’t happen. There are injuries; your body wears out. When you look at a construction site, you’re looking at people kind of like professional athletes—sacrificing their bodies for the trade they’re in.
People do it for their family and their kids. Family is very important, and the skills and pride of the trade are passed down from generation to generation.
Lastly, Mike, you’ve just been reelected as the union’s business manager. You have a new term ahead of you. Four years from now, when you look back, how will you assess whether you were successful?
Mike Silvey: In my position, I have to look out to a longer horizon than four years. We may not see the fruits—or lack thereof—of many decisions I make today for up to 20 years, in terms of whether the trade remains viable in the future. So we may have to wait some time before judging whether I’m successful or not.
That’s what it means to be a steward of a long-standing organization. You take care of it as best you can for today, but you also make damn sure that the things you do today are not going to be a detriment to the organization 10 years from now. You build on what’s behind you, and hope that something better comes after you.
- Log in to post comments