With China no longer accepting imports of post-consumer recyclables from the US, California’s waste facilities are struggling to manage the sudden increase in volume and demand on its waste disposal facilities. Waste-to-energy conversion plants—a staple of European circular economic models to address waste management and reach decarbonization goals— face, despite success in Europe, significant PR & political challenges in US metropoles with air quality issues. To better understand the latest innovative science behind waste-fired power plants globally, TPR recently toured Amager Bakke, a waste-to-energy plant (and, yes, ski slope attraction) in Copenhagen, Denmark; and, spoke with Bettina Kamuk, Global Market Director for Ramboll, who explained how the Copenhagen facility meets air quality and emissions standards while providing low-carbon energy and recreational activity to its surrounding community.
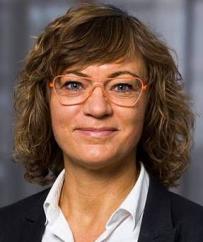
Bettina Kamuk
“The Amager Bakke waste-to-energy (WtE) facility, which we engineered and designed, supplies one-third of all heat to Copenhagen, and is part of Denmark’s 2010 national strategy to reduce all dependency on fossil fuels by 2030.”—Bettina Kamuk
Bettina Kamuk: First, Ramboll is an engineering, design, and consulting firm with 300 offices in 35 countries serving the building, transport, planning and urban design, water, environment and health, energy, and management consulting markets. We, you may know, have 77 offices in the US including Los Angeles and Denver.
The Amager Bakke waste-to-energy (WtE) facility, which we engineered and designed, supplies one-third of all heat to Copenhagen, and is part of Denmark’s 2010 national strategy to reduce all dependency on fossil fuels by 2030. The Amager Bakke WtE facility is owned and operated by Amager Resource Centre (ARC), a five city consortia, to supply low-carbon electricity to 550,000 people and district heating to 140,000 households.
This plant replaced a 45-year-old facility. ARC’s objectives were to replace the aging lines of this facility, produce a lower emission, more efficient plant that would have a higher recovery of materials like metals, and be a beacon for the city, open to the public. Everyone knows that we are building a ski slope on the roof and that this facility is in the center of the city. We don’t hide what we’re doing. We show what we’re doing with our waste.
The combined heat and power producing plant is able to treat up to 560,000 (metric) tons of waste every year from 600,000 inhabitants and 68,000 businesses. Flue gas condensation and heat pumps optimize the production of heat. Consequently, Amager Bakke’s total net energy efficiency is among the highest in the world for a waste-to-energy facility, and it holds a big potential for recycling and recovery.
How much did the facility cost and who paid for it?
The facility cost 3.5 billion Danish Kroner ($525 million). Typical waste-to-energy facilities allocate 30 percent of the cost to the building, but here, the municipalities decided to pay for a really nice building which today is also a tourist attraction. The cost for the facility is paid through a municipal tax. Local law determines how much of the cost of the operation is charged as a gate fee for waste and how much is charged for district heat.
Briefly describe how the Copenhagen waste to energy plant works.
Each day, 250-300 lorries carrying waste arrive at Amager Bakke, where they’re weighed and registered. Recyclable waste is not brought here.
The lorries go to the tipping hall, where they’re unloaded into a 118 foot silo, which holds 22,000 (metric) tons of waste. Two automatic grabbers mix the waste to make it more or less uniform. The grabbers then lift the waste into stoking hoppers for the furnaces. Each grabber can lift up to 15 (metric)tons of waste. Being fully automated, the grabbers can operate 24 hours a day. In order to reduce unpleasant odors, negative pressure is utilized in the tipping hall.
Two identical furnaces have a capacity of 25-35 (metric) tons of waste per hour. It takes 1.5-2 hours to incinerate the waste in the furnace at temperatures ranging from 1740°-1832°F. Once the waste has reached the end of the combustion grate in the furnace, virtually all energy will have been released as hot flue gas.
The furnaces are built together, each with its own boiler, so the hot flue gas from the furnaces transfers its heat energy straight to the water in the boiler pipes. Each boiler can produce up to 137 (metric) tons of steam per hour. The steam from both boilers is collected in a joint steam pipe when it’s channeled into the steam turbine.
The steam turbine is connected to a generator that converts the energy into electricity. Once the turbine has taken the pressure and heat from the steam, there is heat energy left. That energy is used in the district-heat exchangers: district heating water is heated in the heat exchanger and is then sent into the district heating system. The entire process has been designed so that either more heat or electricity can be produced as demand dictates.
How does the Amager Bakke plant manage pollutants from the incineration process?
When the flue gas has passed through the boilers and given off its heat, it must be scrubbed. Each furnace line has a separate flue gas scrubbing system. An electric filter removes most of the dust in the flue gas, also known as fly ash. The flue gas is then passed through a catalyzer, which removes NOx. The first scrubber removes hydrochloric acid, mercury, and other undesirable substances, while the second removes sulphur dioxide using lime. The third scrubber is a so called condensing scrubber. Water vapor is condensed into water droplets so the residual heat can be used in the flue gas with the aid of heat pumps. The residual heat is sent out into the district heating network via heat exchangers. The last stage of cleaning comprises a venturi filter that eliminates the last remnants of particles in the flue gas.
When the waste has been incinerated, 17-20 percent remains as slag. The slag consists of ash from the waste, gravel, sand, metals, and other materials that cannot be incinerated. A maturation process gets particles from heavy metals to bind to the slag particles so they cannot be washed out. Out of 1 (metric) ton of waste, 10-15 kg of metal can be removed and reused from every 200 kg of slag. The slag is screened so it can be used as filler for building and construction work, typically as an under layer for asphalt road construction. The fly ash and other by-products of the smoke scrubbing are used as a substitute for lime to neutralize residual products from other industries.
Additionally, a four stage cleaning and neutralization of wastewater adjusts the pH and removes the remnants of metals and other components.
Lastly, the Amager Bakke plant cuts 100,000 (metric) tons of CO2 emissions per year, and enables the city of Copenhagen to reuse 90 percent of its metal waste, which amounts to 10,000 tons of metal per year. Additionally, the plant will recover 100 million liters of spare water through flue gas condensation and reuse 100,000 (metric) tons of bottom ash, which will be repurposed as road material.
U.S. metropolitan areas with clean air concerns are particularly attuned to managing emissions & pollutants from waste-to-energy plants. How successful have you been in reducing such emissions?
The starting point was that the allowable air emissions should at least meet the Euro Zone baseline. The initial spec was set to 50 percent of that baseline, but the tender to our contractors was that emissions should be even lower. ARC’s operating experience is that we are well below 50 percent. Currently, drinking water from the faucet has higher levels of certain contaminants than the wastewater generated from this operation.
The professionals who manage LA County Public Works have expressed interest in waste- to-energy technologies, but state elected officials have been reluctant to embrace any combustion processes. How has Ramboll responded to such concerns when bidding for U.S. contracts?
We have tried to do our best from a technical perspective to explain what goes on: what are the emissions; are there any risks; are there any issues? We have tried to compare them to other technologies in terms of both cost and reliability and emissions and energy efficiency, and we believe based on all of these comparisons, that combustion technology is a very good idea. We haven’t been able to prove the same good result for the other technologies.
But it is a challenge. I’ve participated in public hearings in the US and Canada. I was invited some years ago for public hearings in Vancouver, and some people you just cannot convince. You have to accept you won’t be able to convince everyone. It’s up to the authority to decide whether they can approve a plant or not. Because many of the people were listening but there was a small group of people demonstrating, with banners and leaflets claiming it was too hazardous to have combustion.
In Europe, I would say we don’t see resistance from the population. In Denmark, Sweden, and Norway, at least, we do not. In the UK, it is becoming more accepted. Ten years ago it was a problem in the UK, but we don’t see the same today. In the US it is very difficult. But also has good examples— In West Palm Beach there was no opposition from the public. And when you see the emission limits here, I think there should be no excuse from an environmental perspective why you should not allow a waste-to-energy facility. If you take a power plant, or the cement industry, the emissions would be far higher.
Lastly, tell us about Copenhagen’s landmark ski slope on Amager Bakke’s roof and the architectural firm, Bjarke Ingels Group (BIG), which designed to building.
True: BIG, the renowned Danish architect, did a good job.
With its sleek ultra-modern design, Amager Bakke will host come this fall one of the world’s longest artificial ski slopes, as well as a café and running path on its roof. It will also include a grove of trees and boasts the world’s tallest artificial climbing wall (85 meters). Around the plant will sit a recreational area with facilities for water sports, soccer fields and a go-kart track.
We, Ramboll, to accommodate the ski-slope, did have to stack the building higher to get the right slope for a +/- 300 meter ski run. We also had to allow for a higher live load factor on the roof for the ski slope, which can accommodate 1,500 people. The ski surface, incidentally, is an artificial plastic material, not snow.
- Log in to post comments